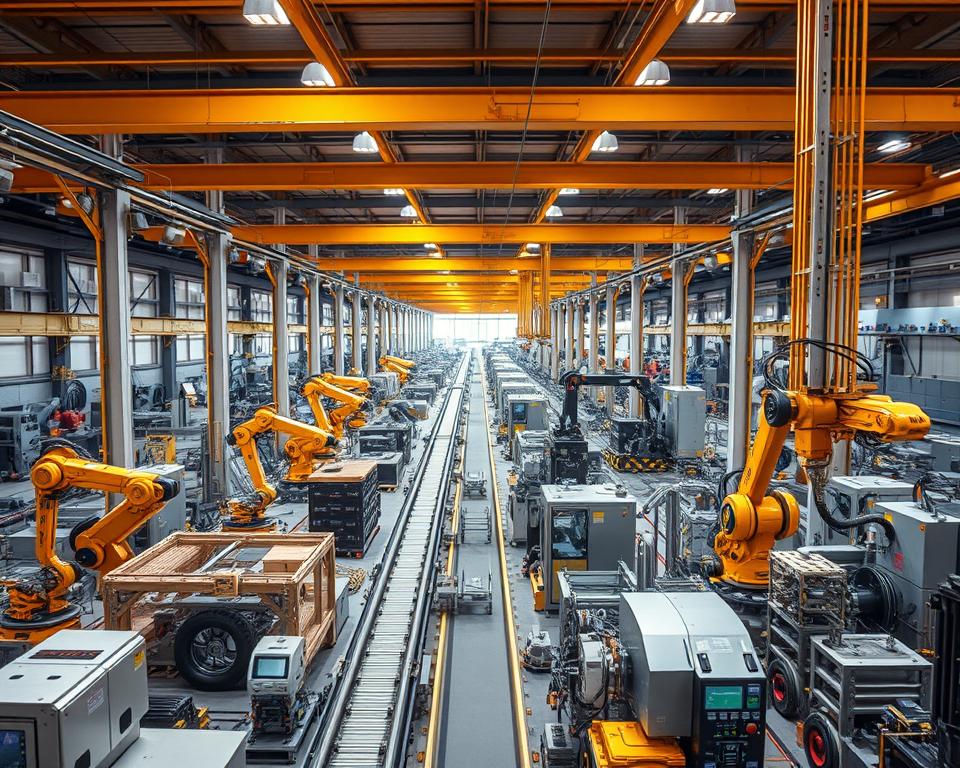
Manufacturing Technology: Innovative Examples
Did you know that 85% of manufacturers believe that embracing advanced manufacturing technologies is crucial for maintaining competitiveness in the global market? As innovation accelerates, manufacturing technology examples abound, showcasing solutions that significantly improve efficiency and productivity across various industries. From robotics to smart systems, these innovative manufacturing solutions are transforming traditional processes and rewriting the rules of production. It’s essential for businesses to stay ahead of the curve by understanding the latest advancements in manufacturing technology and the critical role they play in shaping the future.
Key Takeaways
- 85% of manufacturers prioritize advanced technologies for competitiveness.
- Innovative manufacturing solutions are reshaping production processes.
- Staying updated with trends is essential for success in manufacturing.
- Robotics, AI, and IoT are driving efficiency gains.
- Understanding technology impacts is crucial for future growth.
Introduction to Manufacturing Technology
Manufacturing technology is an essential aspect of industrial production, integrating tools, machinery, and methodologies to facilitate the creation of goods. This field has significantly evolved over the years, adapting to technological advancements and market demands. Understanding what is manufacturing technology helps to appreciate its critical role in our modern economy.
This area of expertise not only enhances productivity but also optimizes resources, resulting in superior product quality. By leveraging various manufacturing technologies, businesses can streamline processes, reduce waste, and accelerate production timelines. The benefits of manufacturing technology extend beyond mere efficiency; they also include improved safety standards and a reduction in human error.
Historically, manufacturing technology has undergone remarkable transformations, from the advent of simple mechanical tools to today’s sophisticated automated systems. These innovations contribute to a more competitive landscape, positioning companies to meet consumer demands swiftly and effectively.
What Makes Manufacturing Technology Innovative
Innovative manufacturing processes define the edge of modern industry, showcasing advancements that enhance production efficiency and responsiveness. The traits that distinguish innovative technology include remarkable flexibility and robust automation capabilities. These characteristics empower manufacturers to adapt quickly to changing market demands without sacrificing quality.
Incorporating cutting-edge digital solutions is essential for any manufacturing operation seeking to thrive. The integration of smart technologies, such as the Internet of Things and artificial intelligence, enables companies to streamline operations, minimize downtime, and optimize resource allocation. Such innovations not only improve production capabilities but also elevate overall competitiveness in the market.
As customer expectations evolve, embracing these characteristics of innovative technology becomes crucial. Businesses that implement these advancements can more effectively meet consumer needs while maintaining high standards of operational excellence. This aligns closely with the ongoing transformation of the manufacturing landscape, ensuring that companies remain relevant and capable of succeeding in a dynamic environment.
Key Trends in Advanced Manufacturing Technologies
The landscape of manufacturing is evolving rapidly, and several key trends are driving this transformation. One prominent shift involves the movement toward smart factories. These facilities leverage Internet of Things (IoT) technology to enhance connectivity among machines and systems, fostering efficient data exchange and analysis. As a result, companies can improve their productivity and respond to market dynamics swiftly.
Another significant trend in manufacturing technology is increased automation. Automation allows for the streamlining of processes, which leads to higher output levels with consistent quality. As labor costs rise, businesses are looking to robotics and automated systems to reduce reliance on human labor, further enhancing competitiveness.
Sustainability has also become a focal point in advanced manufacturing trends. Firms are increasingly adopting practices that mitigate their environmental impact, such as reducing waste and utilizing sustainable materials. This growing focus aligns with consumer demand for environmentally friendly products, positioning companies as leaders in corporate responsibility.
These trends in manufacturing technology not only enhance operational efficiency but also facilitate innovative product development. By embracing these advancements, businesses can maintain a competitive edge and meet the evolving needs of consumers.
Trend | Description | Impact on Productivity |
---|---|---|
Smart Factories | Utilization of IoT technologies to enhance machine connectivity. | Improved efficiency through real-time data analysis. |
Increased Automation | Use of robotics to streamline manufacturing processes. | Higher output with consistent quality and lower costs. |
Sustainability Practices | Adoption of eco-friendly materials and reduction of waste. | Enhanced brand image and alignment with consumer values. |
Manufacturing Technology Examples
Manufacturing technology encompasses a broad range of advancements that are revolutionizing how products are created, assembled, and delivered. Industry leaders are incorporating various technologies to enhance efficiency and adaptability, which leads to significant productivity gains. Below are some key examples that showcase the diversity and potential of modern manufacturing technologies.
Robotics in Production Lines
Robotics in manufacturing has become a cornerstone for many production lines. Integrating robots improves both the speed and accuracy of operations. Companies like Siemens and ABB have successfully implemented robotics to handle repetitive tasks, allowing human workers to focus on more complex problem-solving responsibilities. These systems provide advantages such as reduced labor costs and minimized human error, showcasing effective manufacturing technology examples.
3D Printing Applications
3D printing innovations are transforming the prototyping and production landscape. Businesses can now create intricate parts on-demand, reducing waste and inventory costs. Major brands like Ford and Adidas utilize 3D printers to produce customized components, demonstrating how additive manufacturing can lead to faster product development cycles. This approach also fosters creativity in design, enabling the manufacture of unique products that meet niche market needs.
Smart Manufacturing Systems
Smart manufacturing systems utilize the Internet of Things (IoT) and artificial intelligence (AI) to create interconnected production environments. This integration allows for real-time data analysis, enhancing decision-making processes. Companies like GE and Honeywell leverage these systems to optimize their operations, improve supply chain management, and respond rapidly to changing market demands. The implementation of smart systems represents a significant step forward in creating more agile manufacturing processes.
Digital Manufacturing Techniques Transforming Industries
The advent of digital manufacturing techniques revolutionizes how industries operate. By integrating advanced technologies, companies can vastly improve efficiency, flexibility, and customization. Among these innovations, the role of IoT in manufacturing and AI in manufacturing stands out, driving operational enhancements and offering competitive advantages.
IoT Integration
IoT in manufacturing allows for real-time data collection and monitoring, which leads to better decision-making. Sensors embedded in machinery provide valuable insights into equipment health and production processes. This connectivity not only simplifies inventory management but also enables predictive maintenance, minimizing downtime and reducing operational costs.
Artificial Intelligence in Manufacturing
AI in manufacturing enhances process automation and data analysis capabilities. By utilizing machine learning algorithms, businesses can analyze production patterns and consumer behavior to tailor their offerings. The integration of AI simplifies complex tasks, allowing teams to focus on strategic initiatives and innovative projects.
These digital manufacturing techniques are reshaping the landscape of conventional manufacturing, ensuring that industries remain agile and responsive to market demands. As technology progresses, the importance of integrating IoT and AI becomes more pronounced, ultimately enhancing productivity and product quality.
Cutting-Edge Manufacturing Innovations
In the rapidly evolving manufacturing landscape, cutting-edge manufacturing innovations are reshaping traditional processes. Automation advancements play a central role, streamlining production and improving efficiency on assembly lines. Many companies have embraced robots that not only perform repetitive tasks but also adapt to varying production needs. These automated systems enhance consistency and minimize human errors.
Predictive analytics revolutionizes decision-making for manufacturers. By employing data-driven insights, organizations can anticipate maintenance needs and reduce downtime. This proactive approach leads to significant cost savings and improved operational efficiency.
Customized machinery tailored to specific production requirements represents another profound shift in advanced manufacturing technologies. This flexibility allows companies to quickly modify their manufacturing processes in response to customer demands. As industries continue to adopt these innovations, the potential for growth and competitive advantage expands vastly.
The adoption of cutting-edge manufacturing innovations fosters an environment where efficiency and product quality thrive. Companies integrating these advanced manufacturing technologies are not only enhancing productivity but also setting new benchmarks within their respective markets.
Innovation Type | Description | Benefits |
---|---|---|
Automation Advancements | Integration of robotic systems into production lines | Increased efficiency and reduced error rates |
Predictive Analytics | Using data to forecast maintenance and production needs | Lower downtime and reduced maintenance costs |
Customized Machinery | Machinery developed for specific production tasks | Enhanced flexibility and quick response to market demands |
Benefits of Modern Manufacturing Technologies
The integration of modern manufacturing technologies brings substantial advantages that contribute significantly to industrial sectors. Organizations adopt these innovations primarily to enhance their operations and meet growing market demands. The benefits of modern manufacturing technologies extend beyond mere productivity gains; they encompass a broad range of efficiencies that reshape manufacturing landscapes.
Efficiency and Productivity
Achieving greater efficiency in manufacturing becomes more attainable with the use of advanced technologies. Automation and data analytics streamline processes, allowing companies to optimize resource allocation and minimize downtime. These enhancements lead to more consistent output and higher quality products, which boosts overall productivity. With technology-driven solutions, manufacturers can respond quickly to market changes and customer requirements, ensuring a competitive edge.
Cost Reduction Techniques
Cost reduction strategies are vital for maintaining profitability in today’s market. Modern manufacturing technologies contribute to this through various means, such as waste minimization and energy efficiency. Automated systems help reduce labor costs while improving accuracy, leading to less material waste. Additionally, energy-efficient machines decrease operational costs over time. Emphasizing sustainability can further foster cost-effective practices. Recognizing the benefits of modern manufacturing technologies creates opportunities for businesses to grow while being fiscally responsible.
Emerging Manufacturing Trends to Watch
As the manufacturing landscape evolves, new trends are shaping the way companies approach their processes and customer engagement. Key developments in sustainability and personalization are at the forefront, driving significant changes in production methods and product offerings.
Sustainability in Manufacturing
Sustainability in manufacturing has gained traction as companies prioritize eco-friendly practices. Organizations are increasingly adopting strategies that include waste recycling, energy-efficient processes, and sustainable materials to minimize their environmental impact. These emerging manufacturing trends not only reduce carbon footprints but also appeal to a consumer base that values corporate responsibility. Brands that embrace sustainability often see enhanced loyalty and market differentiation.
Personalization through Technology
Personalization in production allows manufacturers to tailor their products to meet individual customer preferences. This trend leverages advanced technologies such as AI and data analytics, enabling firms to customize outputs based on consumer feedback and behaviors. Personalized production not only enhances customer satisfaction but also drives sales by aligning products more closely with market desires. Companies focused on these personalized approaches are often seen as innovators in their respective fields.
Industrial Technology Solutions for Competitive Advantage
In today’s dynamic market, organizations rely on various industrial technology solutions to secure a competitive advantage in manufacturing. These solutions encompass a range of tools and strategies designed to enhance efficiency, streamline processes, and improve overall productivity.
One prominent example of industrial technology solutions is the integration of automation systems. By automating repetitive tasks, companies not only reduce operational costs but also minimize human error, which can lead to higher product quality. This strategic move plays a crucial role in maintaining a competitive edge.
Another essential component is data analytics. With the ability to collect and analyze vast amounts of data, businesses can make informed decisions that align with market demands. This capability allows for responsive adjustments in production and supply chain processes, directly influencing a company’s ability to adapt quickly to changing consumer preferences.
Additionally, embracing modern manufacturing technologies, such as 3D printing and smart manufacturing systems, opens avenues for innovative product development. These technologies empower companies to quickly prototype and produce customized solutions, further solidifying their competitive advantage in manufacturing.
As organizations continue to evolve, the focus on industrial technology solutions remains pivotal. Companies that effectively leverage these advancements position themselves to thrive amidst increasing competition and rapidly shifting market trends.
Innovative Production Technology: A Case Study
Exploring the landscape of innovative production technology reveals remarkable achievements through industry success stories. Companies have embraced these advancements, leading to increased efficiency, improved product quality, and enhanced customer satisfaction. Analyzing real-world examples highlights the transformative power of cutting-edge technologies in the manufacturing sector.
Success Stories from Industry Leaders
Various case studies in manufacturing demonstrate how industry leaders have successfully implemented innovative production technology. For instance, Ford Motor Company adopted advanced robotics to streamline assembly processes, reducing production time by 30%. This shift not only improved operational efficiency but also enhanced product quality, creating a reliable experience for consumers.
Another notable example involves Siemens, which integrated smart manufacturing systems into its factories. By utilizing IoT devices, Siemens achieved significant real-time data collection and analysis. This initiative resulted in a 20% decrease in energy consumption and a notable improvement in overall throughput.
These industry success stories illustrate how embracing innovative production technology can lead to substantial competitive advantages. Organizations that prioritize these advancements experience enhanced productivity and meet evolving consumer demands more effectively.
Latest Industrial Processes Revolutionizing Manufacturing
The landscape of manufacturing is undergoing a significant transformation powered by the latest industrial processes. Techniques such as lean manufacturing and just-in-time production are taking center stage. These revolutionary manufacturing techniques prioritize efficiency and waste reduction, leading to smoother production flows and improved product quality.
Another remarkable advancement in the industrial sphere is the implementation of digital twins. This technology allows manufacturers to create virtual replicas of physical assets, enabling real-time monitoring and analysis. The insights gleaned from digital twins can lead to enhanced decision-making and predictive maintenance, further optimizing production processes.
Companies are increasingly adopting a modular approach, allowing for more flexibility and scalability. By integrating technological advancements into these latest industrial processes, manufacturers can better respond to market demands while minimizing costs. Embracing these innovative strategies positions businesses to thrive in a competitive environment.
Challenges Facing Modern Manufacturing Technologies
In the evolving landscape of manufacturing, numerous challenges in manufacturing technology impact daily operations. One significant hurdle is workforce adaptation, as employees must adjust to innovative systems and processes. Training and reskilling become integral to overcoming this modern manufacturing issue.
Cybersecurity also looms large. With increased automation and digital integration, vulnerabilities rise. Manufacturers must prioritize robust security measures to protect sensitive data and intellectual property.
Cost of implementation represents another key challenge. Investing in state-of-the-art technologies requires significant capital, which may deter some manufacturers from upgrading. This tension shapes the decision-making process within organizations striving to maintain competitiveness.
Addressing these challenges necessitates strategic planning and a willingness to adapt. By embracing change and investing in capabilities, companies can navigate the complexities of modern manufacturing successfully.
Challenges | Impact | Strategies |
---|---|---|
Workforce Adaptation | Slower implementation of new technologies | On-going training programs |
Cybersecurity | Increased risk of data breaches | Investment in security solutions |
Cost of Implementation | Reduced capacity for innovation | Gradual phased investments |
The Future of Manufacturing: Predictions and Insights
The future of manufacturing faces numerous changes driven by technological innovations and the globalization impact. As industries adapt, manufacturing predictions suggest a transformation in methods and practices. Increased international collaboration has become essential, reshaping supply chains and production processes. These changes are not merely theoretical; they reflect a significant shift in how manufacturing will operate in the coming years.
Impact of Globalization on Manufacturing
Globalization plays a crucial role in defining the landscape of modern manufacturing. Companies now rely on international networks for sourcing materials, producing goods, and delivering services. This interconnectedness fosters efficiency and allows businesses to capitalize on diverse skill sets, which is vital for driving the future of manufacturing.
Manufacturing predictions indicate a continued reliance on global partnerships. By collaborating across borders, companies can effectively manage supply chain disruptions while accessing innovative solutions and technologies from various regions. This adaptability enhances resilience and positions manufacturers to respond to fluctuating market demands.
The ongoing globalization impact is evident in the growth of smart factories and the adoption of advanced technologies. As businesses strive to enhance productivity, they will increasingly integrate IoT and artificial intelligence into their operations. These technological advancements will not only streamline processes but also provide valuable insights for informed decision-making.
Strategies for Implementing Advanced Manufacturing Technologies
Implementing advanced technology in manufacturing requires a structured approach to ensure successful integration and adaptation. Here are several effective strategies for manufacturing technology that can aid organizations in navigating this complex process.
- Conduct a Comprehensive Assessment: Begin with a thorough evaluation of current manufacturing processes, identifying inefficiencies and potential areas for improvement. Understanding the existing framework allows businesses to make informed decisions regarding technology adoption.
- Evaluate Technology Options: Research various advanced technologies, such as automation, robotics, and IoT solutions. Compare their benefits, costs, and compatibility with existing systems to choose the most suitable options.
- Develop a Clear Implementation Plan: Outline specific goals, timelines, and required resources for the technology adoption process. A well-defined plan will help in synchronizing efforts across departments and facilitate a smooth transition.
- Engage and Train Employees: Involve staff in discussions about upcoming changes and provide training on new technologies. Employees should feel supported throughout the transition, ensuring they can adapt to the advanced technology effectively.
- Monitor and Optimize: After implementation, continuously monitor performance and gather feedback. This data helps in identifying further enhancements and ensures that the investment in new technology yields the desired results.
Utilizing these strategies for manufacturing technology can significantly ease the challenges associated with implementing advanced technology. Organizations that take a methodical approach will find opportunities for innovation, increased efficiency, and enhanced competitiveness in the marketplace.
Training and Workforce Development in Manufacturing
As the manufacturing landscape evolves with the introduction of advanced technologies, effective training in manufacturing becomes essential. This includes a commitment to workforce development, ensuring that employees are equipped with the skills necessary to thrive in a competitive environment. Companies must prioritize upskilling manufacturing employees to stay at the forefront of innovation.
Upskilling for the Future
Upskilling manufacturing employees is crucial for adapting to the rapid pace of technological advancement. Organizations benefit significantly when they invest in continuous learning opportunities, empowering workers to enhance their skills and apply new techniques on the job. This investment not only improves employee confidence but also boosts productivity and innovation within the workplace.
Adapting to New Technologies
With the rise of automation and digital tools, training in manufacturing focuses on preparing employees to work seamlessly with these innovations. Companies can implement tailored training programs that emphasize hands-on experience and practical applications of new technologies. By fostering a culture of adaptability, businesses position themselves for long-term success and a sustainable workforce.
How to Choose the Right Manufacturing Technology
Choosing manufacturing technology is a critical decision for any organization looking to optimize performance and meet production goals. The right technology for manufacturing can significantly enhance productivity, reduce costs, and ensure scalability. Understanding your specific needs will help in this process.
First, define your production goals. Consider the volume of products required and the complexity of the manufacturing process. Evaluate whether the technology will allow for flexibility in production and whether it meets current and future demands.
Next, assess budget constraints. Manufacturing technology investments can be substantial, so it’s essential to analyze the return on investment (ROI). A solid financial plan can assist in choosing manufacturing technology that aligns with both short-term and long-term financial objectives.
Lastly, consider scalability options. The manufacturing landscape is constantly evolving, and it is essential to select technology that can adapt to future changes. The right technology for manufacturing should provide room for expansion or modifications without requiring a complete overhaul.
Factor | Description | Importance |
---|---|---|
Production Goals | Define the target output and the types of products. | High |
Budget Constraints | Evaluate the financial resources available for investment. | High |
Scalability | Assess whether the technology can grow with your needs. | Medium |
By thoughtfully considering these factors while choosing manufacturing technology, businesses can maximize their operational efficiency and position themselves favorably in the competitive landscape.
Conclusion
In summary, manufacturing technology is rapidly evolving, showcasing innovative examples that transform how industries operate. The advancements detailed in this article, from robotics to smart manufacturing systems, illuminate the ways in which these technologies enhance efficiency and productivity. As we navigate through challenges and embrace emerging trends, the significance of innovative manufacturing practices becomes all the more apparent.
Looking ahead, the future outlook on manufacturing is bright. Companies that embrace cutting-edge technologies will not only survive but thrive in an ever-competitive landscape. As we continue to adopt digital innovations and foster a culture of upskilling, the manufacturing sector stands poised to redefine its role in the global economy.
Ultimately, this exploration of the summary of manufacturing technology reveals an exciting horizon. Embracing these innovations will empower industries to meet evolving demands, ensuring they remain resilient and responsive to future challenges. The journey toward advanced manufacturing is just beginning, and the possibilities are limitless.